La production est alors mise sous tension: pour rattraper les commandes en retard, les heures supplémentaires s’enchaînent et les expéditions en urgence s’accroissent. La maîtrise passe son temps à revoir la planification de la production et l’atelier ne fait plus confiance aux plannings. N'arrivant pas à satisfaire la demande client, on songe même à investir dans de nouvelles capacités de production (équipements, machines,...) ! Le déséquilibre n'étant pas uniforme, certains services prennent de l'avance sur les commandes client futures et s'attachent à constituer consciencieusement des stocks intermédiaires, au cas où l’avenir leur réserverait de mauvaises surprises.
La production a du mal à répondre aux réclamations client dont le taux ne s'améliore pas: les défauts qualité sont repérés tardivement dans la mesure où les pièces défectueuses sont noyées dans des lots dont la taille ne les rend visibles que bien longtemps après la genèse du défaut.
Face à ces difficultés, quelques initiatives sont lancées ici et là pour améliorer la productivité de tel ou tel service. Malheureusement, ces optimums locaux ne font qu’aggraver la situation (voir théorie des contraintes). En effet, le flux n’étant pas équilibré, les améliorations locales de productivité viennent abonder des stocks intermédiaires que les processus amont ne peuvent exploiter.
Compte tenu des stocks accumulés, les temps de traversée grimpent à tel point que les demandes client ont le temps d’évoluer entre le moment où elles entrent en fabrication et le moment où elles sortent de l’usine !
Les coûts de gestion des stocks (manutentions, inventaires, surfaces), la baisse de productivité globale (augmentation des heures supplémentaires et des heures de main d'œuvre indirecte pour les activités de planification), les coûts engendrés par les retouches, le traitement des réclamations client et les expéditions urgentes viennent augmenter les coûts d'exploitation et réduire un bénéfice, déjà impacté par la contraction des ventes (dans la mesure où la production n'arrive pas à répondre à la demande). Les niveaux de stocks conduisent à augmenter le besoin en fonds de roulement et à mettre sous tension la trésorerie.
La direction commerciale décide alors de lancer une campagne de promotion sur les produits afin de redonner des couleurs au chiffre d'affaires. Les commandes repartent bien à la hausse induisant une forte variabilité de la demande que la production est bien incapable de suivre. Il s'en suit de nouvelles livraisons en retard et des clients toujours plus mécontents.
La situation devient hors de contrôle … il est temps de lancer une démarche d’excellence opérationnelle !
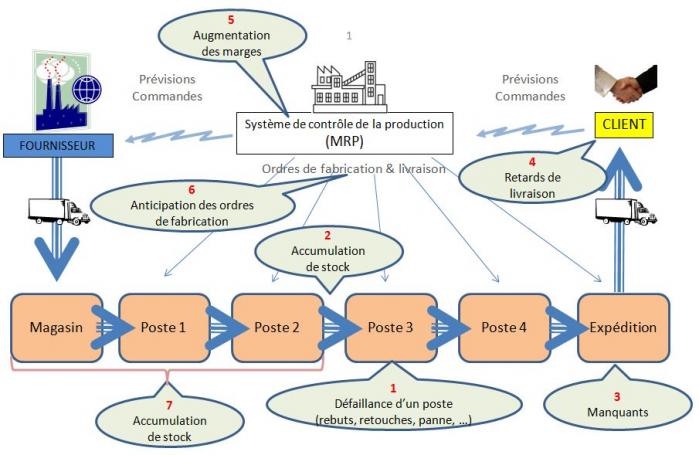
Pour résumer, les principaux symptômes d’une organisation classique n’ayant pas connu de révolution Lean 6-sigma ou de pilotage de la production par les contraintes sont:
· Un sentiment d’urgence permanent,
· Une augmentation de l’en-cours et des stocks,
· Une baisse du taux de service,
· Un taux de qualité en berne,
· De nombreux manquants,
· De nombreuses heures supplémentaires et expéditions urgentes,
· Une augmentation du besoin de fonds de roulement et une trésorerie sous tension,
· Des améliorations locales de la productivité sans aucune incidence sur le chiffre d’affaires,
· Une organisation par service, fonction ou métier ne favorisant pas la fluidité du flux de production,
· La création d'une fonction de chasseur de pièces,
· Des campagnes de promotion que le système de planification de la production est incapable de lisser,
· Des investissements en capacité de production pour répondre à une demande que l'on n'arrive pas à satisfaire.
Voir l'ensemble des billets du BLOG